reliable ceramic foam filter manufacturers
The smelting of aluminum alloy is an important part of the aluminum alloy processing process, which is reflected in the alloying purification and refinement treatment technology in the smelting process. The removal of non-metallic inclusions in aluminum alloy melt by using flux treatment in the furnace and filtration of foam ceramics outside the furnace has long been an important means of aluminum liquid purification.
Foam ceramic is a porous ceramic product with an opening rate of up to 80%, a density of 0.3g/cm32~0.6g/cm3, a unique quasi-stereoscopic network skeleton, and a structure of interpenetrating pores. The earliest foam ceramic filter was successfully developed by China in 1978 and used in aluminum alloy casting systems. In April 1980, their research results were published at the reliable American Foundry Annual Conference. Since then, foam ceramic filter materials have been developed and developed around the world. , widely used in the metallurgical industry.
ceramic foam filter manufacturers (porous ceramic filter) generally use three-dimensional network structures and organic foam plastics with interconnected pores as carriers, which are immersed in a special ceramic slurry with thixotropy, and a special ceramic slurry is used. The rolling process makes the ceramic slurry evenly spread on the skeleton of the carrier, and then it is dried and solidified and then fired at high temperature.
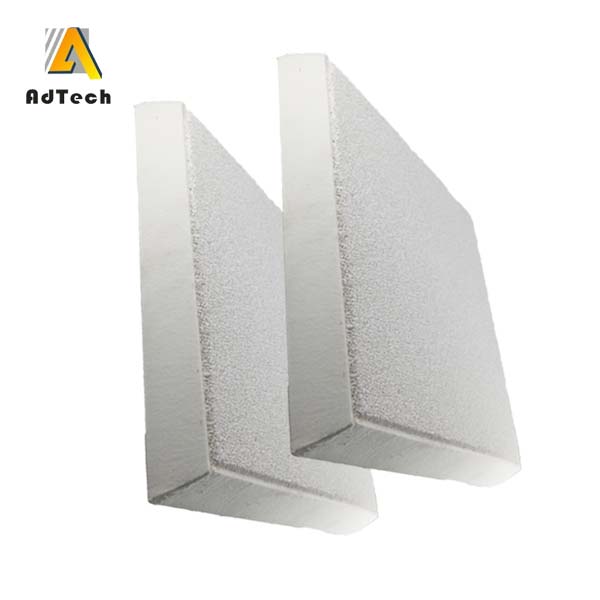
The application of foam ceramic filter plates in the industry has been promoted. There are two application modes for the purification of deformed aluminum alloy melt produced by reliable ceramic foam filter manufacturers: one is to use flux powder to refine the melt in the aluminum alloy semi-continuous casting line in the furnace. , The foam ceramic plate is used for filtering outside the furnace. The ceramic filter plate is to be replaced every time it is cast. Today, some reliable ceramic foam filter manufacturers have also added trough-type online degassing machines before filtration to improve the purification effect; the second is in the continuous casting and rolling line. The replacement cycle is determined according to the force of the filter plate. As for the size of the filter plate selected, it is determined according to the unit time flow of molten aluminum and the total amount of molten aluminum; the selection of foam ceramic filter plates with the most apertures is determined according to the cleanliness requirements of the final molten aluminum. The higher the cleanliness requirement, the smaller the selected pore size. The filtration and purification of foam ceramics is the last process of aluminum liquid purification. Before this process, flux powder spraying refining or online rotary degassing is used, so the impurity phase hydrogen that has not been removed in the aluminum liquid is The particles are more subtle and diffuse. How to promote the accumulation and growth of the impurity phase and hydrogen adsorption in the filtration of foam ceramics is particularly important. The mechanical interception of the “filter cake” effect of foam ceramics alone cannot achieve outstanding results. The new generation of foam ceramic filter material is the research of this subject.