Aluminum ceramic foundry filters are affected by magnetic fields
1 Introduction
Premium quality aluminum castings require a high level of metal cleanliness and are crucial for critical structural components. The development of more efficient filtration methods for liquid aluminum is therefore essential to producing very clean aluminum. i.e. have conditions that allow particulates down to 10 um to be removed. As a result, the particulate removal efficiency of porous ceramic filters has become a subject of interest.
The generation of a magnetic field by an induction coil in combination with an Aluminum ceramic foundry filters causes circulation of thee to melt through the filter media modifying the inch separation. Applying an alternating magnetic field produced by a solenoid haslearly several advantages, i.e. ( 1 ) avoidance of contamination by physical contact with the stirring device, ( ii ) no sub-cooling during filtration, ( iii ) better priming of the filter element with a lower metallic head, and ( iv ) subsequently higher casting rates for high pores per inch ( PPI ) filter grades.
In the present study the influence of the magnetic field on the priming and wetting ability that the aluminum alloy A356 has on the ceramic surface of the Aluminum ceramic foundry filters will be studied, as well as the possible impact it may have on the filtration mechanisms inside the ceramic filters by analyzing the distribution of the 1323 um SIC particles 2-D axial symmetric COMSOL( Version 4 . 2 ) models and analytical modeling will be performed to estimate the heat and Lorentz forces produced, as well as to study the flow pattern induced the melt inside of the filter elements
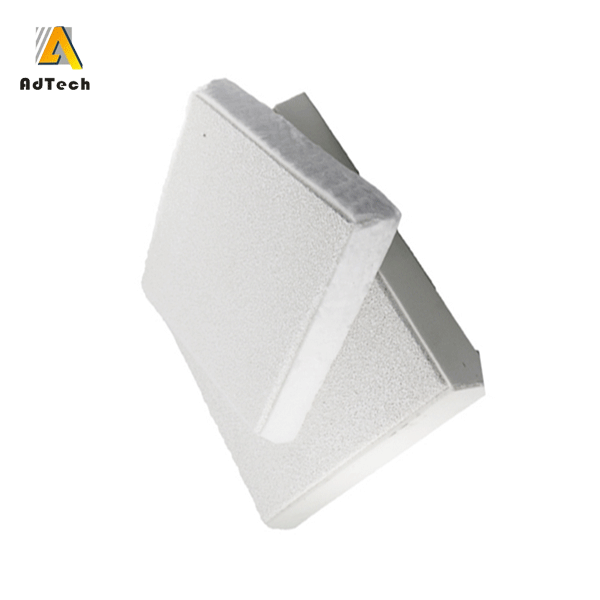
2 Materials and Experimental Methods
In the present experimental setup, the time-varying magnetic field induces currents in the molten metal that is contained in the apparatus. The cross product of the induced current and the magnetic field generates in turn a magnetic pressure, and the gradient of the flux density along the axis of the coil creates a pressure gradient. The pressure gradient results in curl which then induces a bulk flow in the metal. The curl of the Lorentz force is highly dependent on the conductivity of the metal and the effective conductivity of the metal within the Aluminum ceramic foundry filters, which is reduced due to the tortuosity and porosity of the filter. The induced liquid metal velocity within the Aluminum ceramic foundry filters can be determined by using the fluid permeability of the filter media. Due to the high induced velocity within the filter both the Darcian and Non-darcianpermeability terms are required to be solved for the resulting flow field using a Finite Element Model( FEM ). A review of the pertinent theory2, the experimental development, and the validation – “of the COMSOL ” induction heating / magnetic field model ” has already been published earlier by members of the present research group. The details of the model computations are beyond the scope of the present paper and can be found elsewhere.