metal based boron nitride coating for casting high and stable quality.
Titanium and titanium alloys have been widely used in important fields such as aerospace, energy, and marine transportation due to their low density, high specific strength, wide operating temperature range, and corrosion resistance. However, the high production cost and difficult processing of titanium alloy parts limit the wide application of titanium alloy products in the national economy.
Titanium alloy investment casting is one of the important methods to reduce the manufacturing cost of titanium alloy parts. The use of investment casting technology to make titanium alloy net precision castings with no allowance and less machining is a successful technical route for people to explore and reduce the production cost of titanium alloy parts. However, due to the high reactivity of titanium at high temperatures, it reacts very quickly with oxygen, nitrogen, hydrogen, and carbon in a liquid state, and can react with almost all refractory materials. Commonly used refractory materials such as corundum, quartz, magnesia, cobalt sand, etc. will react violently with molten titanium, and cannot be used as surface layer modeling materials for investment casting shells of titanium alloys. Yttrium oxide, zirconium oxide, or tungsten powder with high chemical stability are commonly used modeling materials in titanium alloy investment casting. Although the surface reaction layer of castings produced by using these materials as surface layers is small, these materials There are also problems such as high price and complicated production process.
The structure of bn coating with stable quality is similar to graphite, and its appearance is white, commonly known as white graphite. Its chemical properties are very stable. It has no wettability to most metals and does not react. Zhao Fengminghui et al. It has been found that pyrolysis can be used for melting titanium alloys, and the scour loss of molten titanium liquid is small for pyrolysis. Therefore, this paper discusses the use of hexagonal metal-based boron nitride coating as the surface layer modeling material of titanium alloy investment casting for casting high-quality and stable surface layer modeling materials, mainly to study the interface reaction between titanium alloy and mold shell and its reaction mechanism.
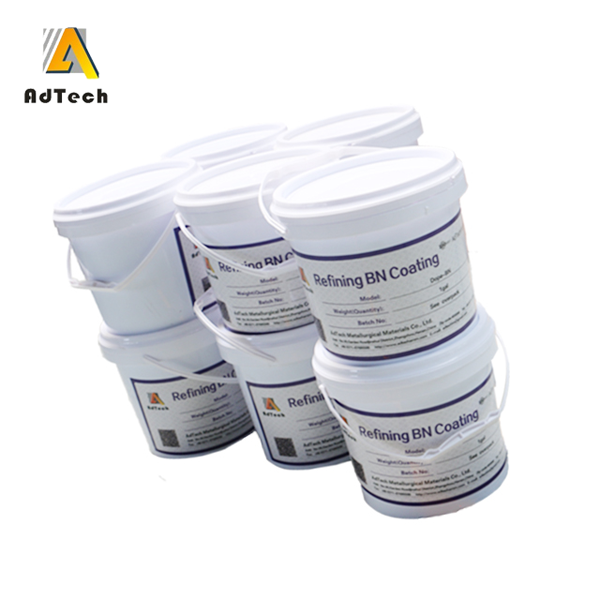
1 Sample preparation
metal based boron nitride coating for casting high and stable quality powder used in the test was provided by a company in Beijing, and its main indicators are shown in Table 1. The preparation process of the metal-based boron nitride coating for casting high and stable quality bn coating composite shell is as follows: according to the ratio of Table 2, the treated boron nitride, yttrium oxide, and a small number of additives (JFC type surfactant, octanol) are put into the yttrium sol, and the coating is prepared. metal based boron nitride coating for casting high and stable quality is evenly coated and hung on the surface of the wax type, sprinkled with 100-mesh yttrium oxide sand, and repeated once after the coating is fully dried; The composition of silica sol (see Table 2 for the ratio), the back layer was sanded with 40-mesh and 20-mesh mullite sand and repeated five times. After the shell was fully dried, the shell was dewaxed using a microwave oven; The shell was heated to 850°C in a roasting furnace for 2 h and cooled with the furnace.