The upstream enterprises in the alloy additives industry are mainly metal raw material suppliers. The company mainly directly purchases pure metal materials and makes powders such as electrolytic manganese, electrolytic aluminum, and metallic silicon, or directly purchases metal powder materials such as metallic iron powder and metallic aluminum Powder and other deep processing. The industry has strong professionalism, adequate market competition, and stable supply, but the cost of industrial products is affected by the price fluctuations of related metal raw materials and chemical raw materials.
The downstream industries of this industry are mainly metal alloy manufacturing enterprises. Metal alloy products are widely used in military aerospace, automotive transportation, shipbuilding, metal material packaging, 3D printing and other industries. The market demand of downstream industries directly affects the company’s products. It has an impact, but because the company’s products are used in a wide range of industries, it will not rely excessively on the market demand of a single industry, and the industry demand is relatively stable. AdTech offers various alloy additives for aluminum foundry, such as Ti additive, Cu additive, Fe additive, Mn additive, Cr additive.
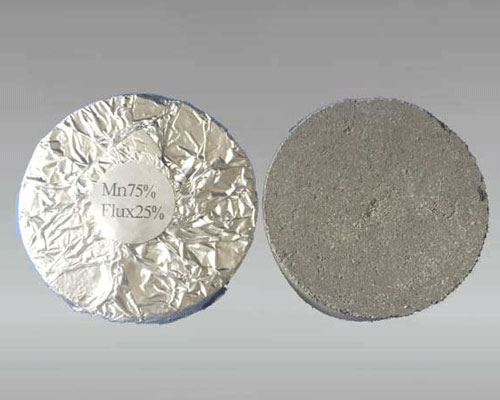
Alloy Element Additives Industry Barriers
(1) Technical barriers
The alloy additives manufacturing industry is a technology-intensive industry. The products of this industry have undergone repeated program design, repeated testing, data analysis, production inspection, and gradually revised the experimental results to form a stable, which can quickly melt in a few minutes. Products with high recovery rate. At the same time, in addition to possessing high-quality talents with rich knowledge reserves in materials science, metallurgy, chemistry, etc. in the industry, they also need to have rich experience in the industry, long-term experimental accumulation, continuous R&D investment, etc. Technical barriers in the industry.
(2) Capital barriers
The alloy additives manufacturing industry is a capital-intensive industry. First of all, the prices of raw materials used in the industry are high, and the production of products requires a lot of capital. Secondly, a large amount of experimental analysis and long-term R&D investment, as well as production equipment and analysis and testing experimental equipment, need sufficient financial support. In addition, the cultivation of talents also requires a large amount of capital; at the same time, as the competition in the industry becomes increasingly fierce, and related technologies and products are updated rapidly, a large amount of capital needs to be invested to promote technological upgrading and research and development of high-tech value-added new products. Therefore, investors who intend to enter the manufacturing industry of alloying element additives and nonferrous metals must have a strong capital scale and financing capability.
(3) Qualification barriers
First, entering the metal alloy additive manufacturing industry requires obtaining a corresponding qualification license. At the same time, downstream customers in the industry, such as the world’s top 500 companies, have strict qualification requirements for supplier selection. Under normal circumstances, to become a stable supplier, industry companies need to provide analysis and testing samples, on-site inspection and evaluation, provide test samples, provide test products, quality approval, supplier qualification determination, etc. for about 1-2 years. Complex authentication process. But once the industry enterprises have established long-term good cooperation with them, they will not be easily replaced. Therefore, industry companies need to form long-term stable performance and produce high-quality products to gain customer trust and successfully pass customer supplier certification, which are not achievable in a short time.
(4) Barriers to intellectual property protection
Through years of technical research and development, industry companies have formed numerous patented technologies in production formulas, manufacturing processes, and testing methods. It is difficult for new entrants to enter the industry with their own new patented technology. At the same time, the use of relatively backward technologies will be at a competitive disadvantage in terms of environmental protection, quality, and cost.