The aluminum Machined Ceramic Foam used in the filtration of liquid casting alloys should have the following properties: ① have suitable refractoriness and low thermal expansion coefficient so that it will not soften, deform and crack under the long-term action of high-temperature molten metal; ② have sufficient Mechanical strength at room temperature and high temperature so that it can withstand vibration during transportation, extrusion, and impact of high-temperature molten metal during use; 3. Excellent high-temperature chemical stability, so that it will not be eroded by high-temperature molten metal and avoid contamination of the metal liquid.
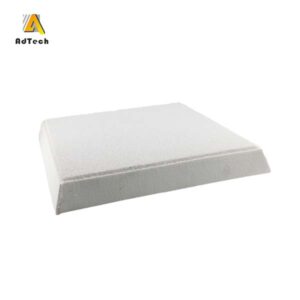
1.21 Overview of the development of porous ceramic filter materials abroad The earliest Aluminum Machined Ceramic Foam was the foam ceramic filter for aluminum alloys developed by Mollard and Davison of Consolidated Aluminum Company of the United States in 1978, and its trade name was Selee/Al. In 1984, the foam ceramic filter Sele/re for filtering ferrous metals was developed. Selee/Al is a bonded corundum filter with aluminum phosphate (APO) as the binder. Its maximum service temperature is 1400 ° C, and it can also be used for other non-ferrous alloys. Hi-Tech Ceramics Co., Ltd. in the United States in the 1980s. In the early stage, four kinds of Aluminum Machined Ceramic Foam for filtering superalloys were successfully developed, and their refractory aggregates were mullite, corundum, and zirconia toughened corundum (GTA) and magnesia partially stabilized zirconia (PSZ). The refractoriness of the filter is 1650~-1800℃, the average pore size is Φ0.5~1mm, the thickness of the skeleton is 0.23~0.69mm, and the high temperature creep (the deformation amount per hour of the sample under 0.034MPa and 1500℃) ) is 0.074~0.749%/h, and the filtration efficiency is as high as 92~99%. American Astromet also produces foam ceramic filters for the filtration of aluminum, magnesium, copper, cast iron, cast steel, stainless steel, and other alloys. The material is mainly Corundum, and zirconia mixed with titanium oxide and silicon dioxide, etc. The company’s research shows that: the foam ceramic filter bonded with phosphate or chromate will crack in the range of 1093~1260 °C; Although the sintered filter has good thermal shock resistance, it softens at around 1593 ° C; these two types of Aluminum Machined Ceramic Foam is generally not suitable or less used for filtration of cast steel and cast iron alloys. The United States has also successfully developed SiC- Al2O3 composite material sintered ductile iron filtration foam ceramic filter, its composition is: 50wt% siC, 40wt% AlO3, and the rest are sintering aids, binders, etc. Formerly the largest manufacturer of porous ceramics in the world, Astro and Selee Corporation of the United States, Self-produced foamed plastic precursors, formed by dipping roll forming machine, the green body is microwave drying, high-temperature roller kiln is continuously fired by computer monitoring, detection and packaging have been fully mechanized, the entire production process has reached high technical level japan has also developed rapidly in the development and application of ceramic foam filters for casting, and its materials are cordierite (O2), mullite (and so on. Japan Toshiba Ceramics Co., Ltd. (Toshiba) applied to Germany in 1987. Foam ceramics The Aluminum Machined Ceramic Foam patent is made of SiN4, with more than 1wt% of Al2O3, SiO2, TiO2, MgO, zrO2, and Cr2O3 as sintering aids. is 11MPa: when there is no sintering aid, the compressive strength is only 1MPa.