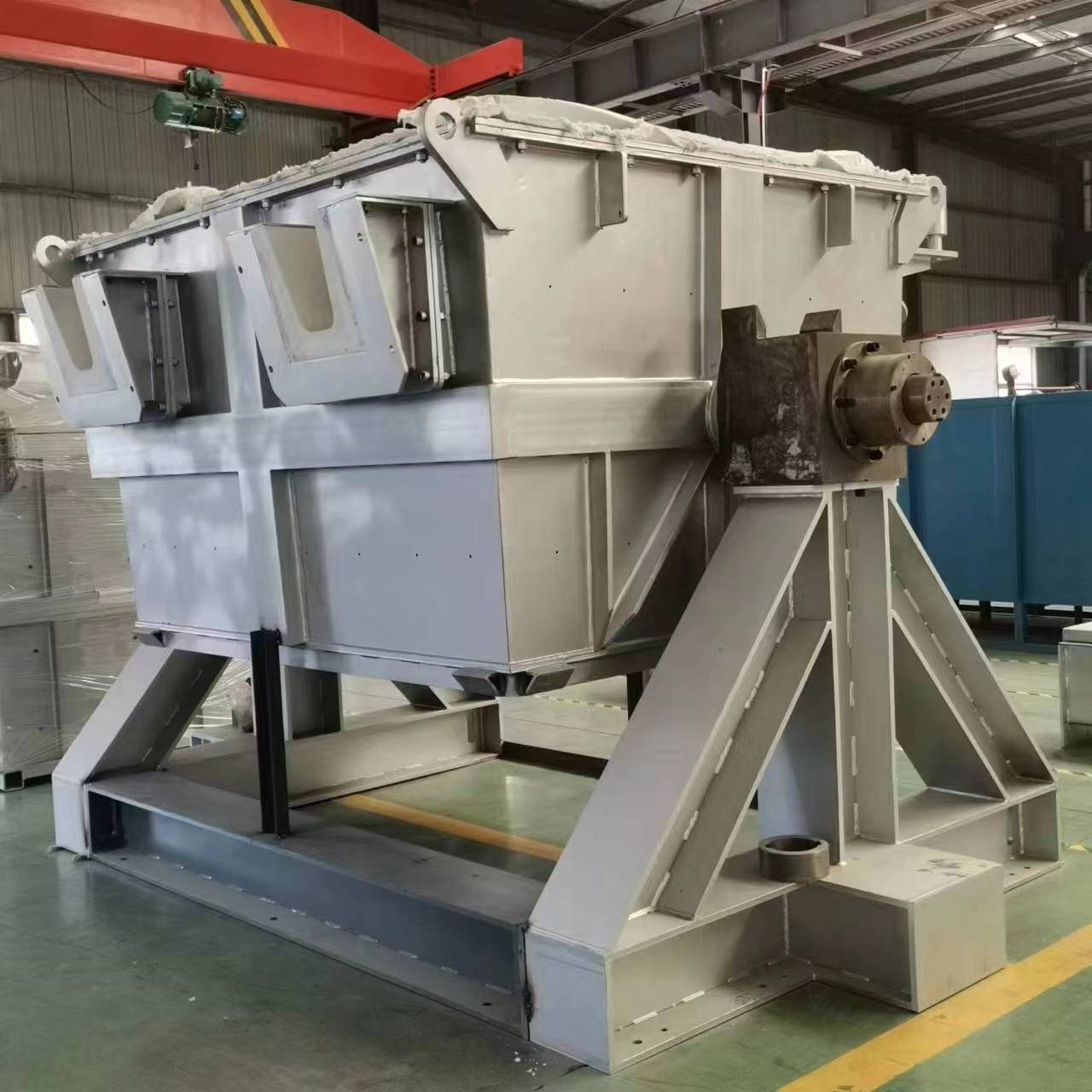
Another measure of foam performance is the porosity of the foam, which is the ratio of the volume of the open cells of the foam to the volume of the entire foam, usually expressed as a percentage. Practice shows that the porosity of the same foam with different PPI is very close. The calculation method of porosity is as follows.
P=(A-B)/A x 100%
P-Porosity
A-Foam weight without open cells
B-Foam weight after opening
Figure 1: Schematic diagram of foam specifications
Figure 2: Schematic diagram of the airflow method
Table 1: Examples of pores of different sizes of 17” foam
In addition to the problems mentioned above, domestic foams also have holes of different sizes and irregular shapes. Therefore, when the same piece of foam is cut in different directions, the surface will show different “PPI”, and the same piece of foam will appear on different surfaces. The pore size is also different. At present, there is no instrument for measuring the air permeability of foam in China. The foam specification still uses the traditional measurement method. The foam specification provided by the manufacturer can only be used as a reference. degassing unit
1.2 The mechanical properties and surface quality of the mud ceramic filter plate have a direct relationship with the mud. The general requirements for the mud for making the porous ceramic filter: (1) It should have a suitable viscosity, if the viscosity is too low, and the mud absorbed by the foam is insufficient, it will make the filter plate The strength decreases and the specific gravity decreases; although the viscosity is too high, the strength can be improved, but it will cause too many dead pores, and even cause the surface to drop slag. If it is too high or too low, it should be adjusted in time. (2) The mud should have a certain fluidity to ensure that the mud is easy to squeeze in and out when the foam is impregnated. (3) The main raw materials that make up the mud should have a certain degree of hydrophilicity to ensure that the mud forms a uniform suspended glue. If the hydrophilicity is poor, the solids in the mud will easily precipitate and stay in the foam during the dipping process, resulting in dead pores and increased brittleness of the filter plate. The specifications of the ingredients and raw materials have a decisive influence on the performance of the mud. Even if the same raw material has slightly different specifications, the deformation resistance, compressive strength and surface brittleness of the finished products will be very different.