The research and development of foam ceramic filters for casting in the UK also started earlier. In the early 1980s, the famous British company Foseco successfully developed a foam ceramic filter (model sⅳvex) for filtering non-ferrous alloys (especially aluminum-based and copper-based alloys) and filtering most of the cast iron and some high melting points. Copper alloy foam ceramic filter (model Sedex). Filtered aluminum alloy die castings have 50% less tool wear when machined than unfiltered castings. Filtration can increase the fatigue strength of ferrite ductile iron by about 10%, and reduce tool wear by 0.04~0.1mm; after the ductile iron box body adopts filtration technology, due to the simplification of the gating system, the casting process yield is increased from 39% to 0.1mm. 63%. By the late 1980s, Foseco introduced a ceramic foam filter (model Telex) for filtering steel castings, with an open porosity of about 70%. It was Rolls-Royce of Fairey Ceramics in the UK that was awarded the first patent for a foam ceramic filter in the UK. The company’s foam ceramic filter can be used for aluminum, and copper-magnesium alloy, but not for molten steel filtration. In the late 1980s, the use of foam ceramic filters in the British aviation industry casting production reached as high as 25,000 pieces per month.
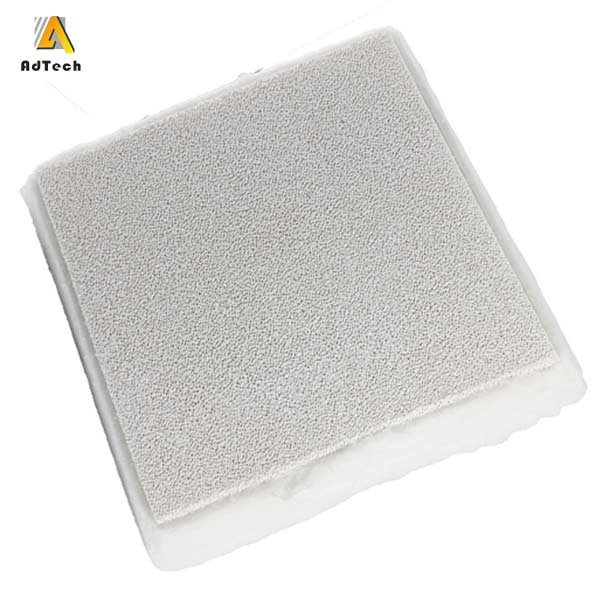
In addition to the United States, Japan, the United Kingdom, Germany and Switzerland, and other countries have also successfully developed ceramic foam filters for casting alloy filtration, and have been widely used in sand casting, die casting, investment casting, and other castings of various materials. The material composition of a foam ceramic filter patent obtained by Swiss Aluminium Co., Ltd. in 1988 is more than 50wt% SiC, more than 30w% SiO2, and the rest is Al2O3. Among them, SiO2 is used as a colloidal binder. This foam ceramic filter is mainly used for the filtration of cast iron alloys.
1.22 Development Overview of Porous Ceramic Filter Materials in China
The research work on porous ceramics began in my country in the early 1980s. In the past 20 years, more than a dozen scientific research institutions and manufacturers have carried out exploration and research on porous ceramic products.
how to make ceramic foam. The filter for ferrous metal (CFF-I type) developed by Harbin University of Science and Technology in the mid-1980s uses high alumina bauxite as refractory aggregate. After that, a CFF II filter was developed by adding a small amount of Y2O3 and CeO2 as sintering aids. The sintering holding time was shortened from the original several hours to about 10 minutes, and the sintering temperature was also reduced by about 200 ℃, but the performance of the product did not change. big. To improve the ability of the foam ceramic filter to resist brittle failure when filtering superalloys, the school also added zrO2 toughening agent and TO2, refractory clay, and other sintering aids to the corundum powder base material, and used aluminum dihydrogen phosphate as the adhesive. The foamed ceramic filter for cast steel was developed at a sintering temperature of 1560 ℃, and its main physical properties were significantly improved. The proofreading of various molten metal filtration tests shows that the foam ceramic filter can effectively remove non-metallic inclusions and other slag inclusions and part of the gas, improve the metallographic structure of the casting and refine the grains, and can increase the tensile strength of the aluminum alloy by 4 ~5%, elongation increased by 7~11%: the tensile strength of the copper alloy can be increased by 22%, the elongation can be increased by nearly double, and the hardness can be increased by 8~20HB: the flexural strength of gray iron can be increased by about 5%. The tensile strength is increased by about 16%; the tensile strength of ductile iron can be increased by about 17%, the elongation rate can be increased by about 40%, the hardness can be increased by about 10%, and the hardness distribution is more uniform; the elongation rate of stainless steel can be increased by 67%, and the impact toughness can be increased by 67%. 18% increase.